ASSAB Tool Steel Solution: Supporting the Rise of Magnesium in Automotive Manufacture
-1024x576.jpg)
The inherent lightweight properties of magnesium make it ideal for automotive applications, especially in electric vehicles (EVs), where reducing weight enhances performance and efficiency. Its parts are approximately 34% lighter than aluminium, providing significant weight reduction benefits.
As magnesium alloys continue to gain traction in the automotive industry due to their lightweighting benefits, ASSAB’s advanced steel solutions play a crucial role in supporting the efficient and sustainable use of magnesium in manufacturing. Known for producing high-performance tool steels, ASSAB’s products are instrumental in addressing the challenges associated with magnesium processing geometries.
Case Example: Dievar Used for Magnesium Instrumental Panel
- Product: Magnesium instrumental panel
- Work Material: Magnesium
- Work Temp. (°C): 660-680
- Process: Die Casting
- Lubricant (if any): Water based spray
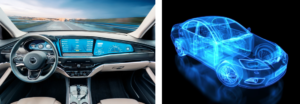
Dievar was used for producing magnesium instrumental panel for an automotive application. It demonstrated a remarkable improvement in tool life. In this particular case, the tool life of Dievar was found to be twice as long as that of H13 steel, significantly reducing maintenance costs and downtime for the manufacturer.
Tool Steel | H13 | DIEVAR |
---|---|---|
Hardness | HRC 46-48 | HRC 46-48 |
Shots/Maintenance | 20,000 | 20,000 |
Total Tool Life | 100,000+ | 200,000+ |
Failure Mode | Erosion/crack | Erosion/crack |
The extended tool life of Dievar not only contributed to higher production efficiency but also reduced the overall cost-per-part in magnesium component production. With a more durable tool, the manufacturer was able to maintain consistent part quality over a longer period, ultimately leading to cost savings and enhanced production capabilities for magnesium parts.
1. Improved Tooling Durability for Thixomoulding
Thixomoulding is a one-step, semi-solid moulding technique in which magnesium alloy chips are heated and transformed into a semi-solid state before being injected into a mould cavity to produce parts with intricate.
Thixomoulding requires precise temperature control and robust tooling to achieve high-quality results. ASSAB’s speciality steels, with excellent hot strength and wear resistance, provide the necessary durability to withstand the challenges of Thixomoulding. The longer tool life offered by ASSAB’s steels reduces maintenance costs and downtime, leading to improved productivity. Additionally, with tools that last longer, manufacturers can significantly lower the cost-per-part, enhancing the economic feasibility of magnesium adoption in large-scale automotive production.
2. Supporting the Transition to Larger Magnesium Components
The rise of electric vehicles (EVs) and other automotive applications demands larger and more complex magnesium components. To meet these needs, die-casting technology is scaling up, and tools must withstand greater mechanical stress. ASSAB’s steels, such as Dievar, are specifically engineered to endure intense thermal cycling and mechanical stress, essential for producing large magnesium parts like motor housings, battery enclosures, and underbody components. By utilising ASSAB’s advanced steels, manufacturers can produce large-scale, complex magnesium parts with minimal risk of tool failure, ensuring the reliable production of these critical components.
3. Sustainability Through Longer Tool Life and Reduced Waste
In line with the automotive industry’s increasing focus on sustainability, ASSAB steel solutions help extending the tool life, reducing the frequency of tool replacements and the environmental impact of manufacturing. Longer-lasting tools reduce the need for raw material inputs, minimise waste, and reduce the carbon footprint associated with tool production and disposal. Furthermore, because ASSAB steels are manufactured to the highest precision and quality standards, they help maintaining the dimensional accuracy of the parts being produced, contributing to more efficient raw material usage and reducing scrap.
4. Bridging the Gap Between Magnesium and Aluminium Components
As magnesium alloys are increasingly adopted for lightweight structural components, aluminium remains a critical lightweight material in automotive manufacturing, particularly in areas that require higher strength and durability. ASSAB’s versatile steel solutions allow for seamless integration between magnesium and aluminium components in hybrid or multi-material assemblies. This integration ensures that vehicle structures to maintain their strength while achieving significant weight reductions. For instance, aluminium components like battery housing using thixo overmoulding work in harmony with magnesium parts to balance strength and lightweight properties, optimising overall vehicle performance.
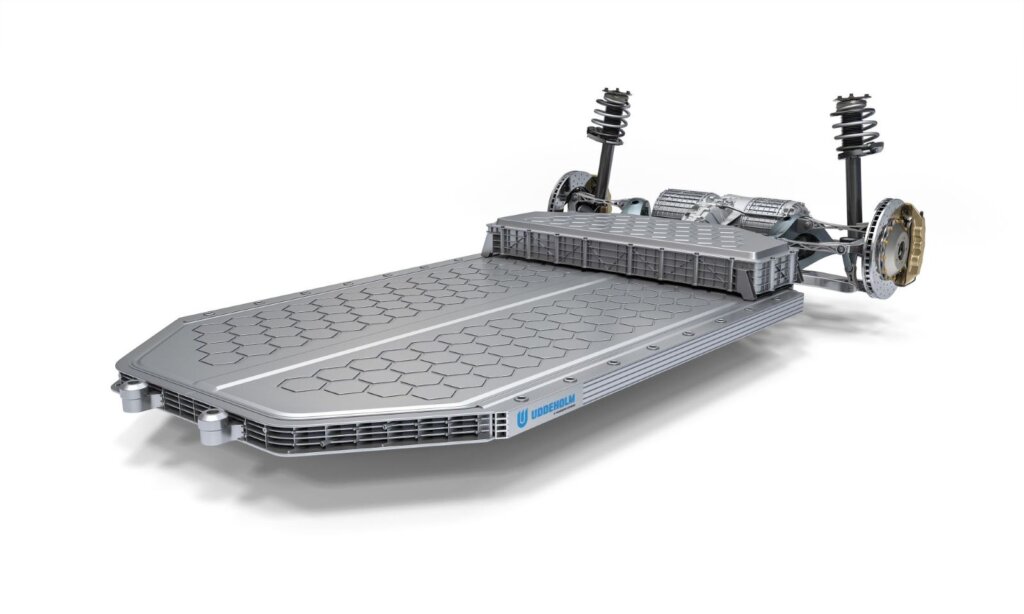
Summing Up
As the automotive industry continues to embrace magnesium alloys for lightweighting and performance enhancement, ASSAB advanced steel solutions offer a critical advantage in overcoming the challenges of magnesium processing. By providing high-performance tooling materials like Dievar, which withstand extreme conditions and provide extended tool life, ASSAB ensures the efficient, cost-effective, and sustainable use of magnesium in automotive manufacturing. With a strong focus on tool longevity, precision, and durability, ASSAB steel products are essential in supporting the widespread adoption of magnesium alloys and ensuring that the automotive industry can meet the demands of tomorrow’s lightweight, high-performance vehicles. Together, steel and magnesium are paving the way for the next generation of automotive innovation.